TOOL AND HARDWARE INDUSTRY
The tool and hardware industry is a vital sector where forging for tool and hardware industry applications plays a pivotal role in the production of high-strength, durable tools and components used in various applications. Forged products are preferred in this industry due to their superior mechanical properties, which include increased strength, durability, and resistance to wear and fatigue. From hand tools such as wrenches, hammers, and pliers to industrial-grade hardware like fasteners, bolts, and heavy-duty cutting tools, forged components are essential for ensuring reliability, precision, and safety in everyday use. The forging process, by its very nature, allows for the manufacture of tools and hardware that can withstand extreme pressure, high impact, and prolonged use without failure, making it the method of choice for critical components in this sector. In this comprehensive analysis, we will explore the various applications of forging in the tool and hardware industry and explain why forged products are integral to the performance and success of this sector.

1.Forged Hand Tools: Strength and Durability
One of the most recognizable applications of forging in the tool and hardware industry is the production of hand tools. Tools such as hammers, wrenches, pliers, and screwdrivers are often subjected to high-impact forces and need to be extremely strong to avoid breaking or deforming during use. Forging is the ideal manufacturing process for producing these tools because it aligns the grain structure of the metal, enhancing the strength and durability of the final product.
For example, a forged hammer head is much stronger than one that has been cast or machined. The forging process compacts the metal and refines its structure, which increases its resistance to wear and impact. This is crucial for a tool that is repeatedly struck against hard surfaces, as the material needs to maintain its integrity over time. Similarly, wrenches and pliers, which are used to apply torque to fasteners or grip objects tightly, benefit from the superior mechanical properties imparted by forging. These tools must endure significant forces without bending, breaking, or losing their shape, and the forging process ensures they can meet these demands.
Moreover, the superior toughness of forged hand tools allows them to perform reliably even in harsh working environments, such as construction sites, factories, and automotive repair shops, where they are exposed to extreme conditions. This long-lasting durability reduces the need for frequent tool replacements, saving time and money for both professional and DIY users.
2.Forged Fasteners and Connectors: Essential for Structural Integrity
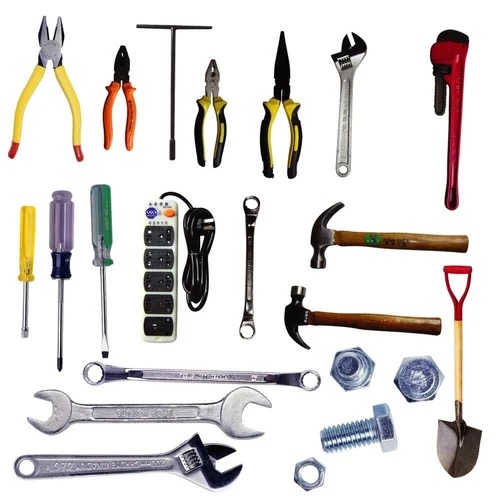
Furthermore, forged fasteners are used in highly demanding environments such as oil rigs, bridges, and industrial machinery where reliability is essential. These components are often exposed to harsh environmental conditions, including high temperatures, corrosion, and pressure. Forged fasteners, made from high-quality materials like stainless steel and alloy steel, can withstand these challenges while maintaining their strength and functionality. This makes them indispensable in the tool and hardware industry, where performance and safety are critical considerations.
3. Cutting Tools: Precision and Longevity
Forging is also heavily utilized in the production of cutting tools such as blades, chisels, and drill bits. These tools are required to maintain sharp edges and precision over prolonged periods, even when used on tough materials like metal, wood, or stone. Forging provides the necessary hardness and wear resistance to ensure that cutting tools remain sharp and effective over time.
For example, forged chisels used in woodworking or metalworking maintain their cutting edge longer than those made through other manufacturing methods. The forging process not only enhances the hardness of the chisel but also aligns the grain flow in a way that reduces the likelihood of chipping or dulling. This translates to increased efficiency for users, as they can complete tasks faster and with greater accuracy.
Similarly, drill bits, which are used to bore holes in materials, benefit significantly from forging. The high rotational speeds and pressure applied during drilling generate heat and wear, which can quickly degrade lower-quality tools. Forged drill bits are designed to handle these extreme conditions, retaining their sharpness and structural integrity even after repeated use. This makes forged cutting tools the preferred choice for professionals in industries such as construction, manufacturing, and automotive repair, where precision and reliability are paramount.
4. Heavy-Duty Hardware: Load-Bearing Capacity
The tool and hardware industry also encompasses a wide range of heavy-duty hardware products, such as hooks, chains, lifting equipment, and rigging components, all of which require high load-bearing capacity and resistance to wear. These components are essential in industries such as construction, mining, and transportation, where they are used to lift, secure, and move heavy loads. Forged hardware is prized in these applications because of its superior strength and toughness, which allow it to handle extreme forces without failure. .For example, forged hooks and chains are commonly used in cranes, hoists, and other lifting equipment to move heavy materials. The forging process enhances the strength and fatigue resistance of these components, ensuring that they can handle the repeated stresses of lifting and lowering heavy loads without breaking or deforming. This is critical in applications where safety is a major concern, as a failure in lifting equipment can result in serious accidents.
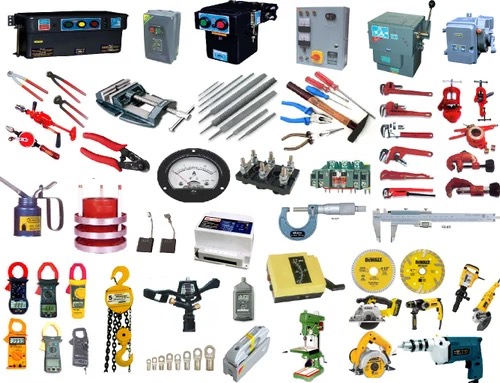
Similarly, rigging components such as shackles, turnbuckles, and eye bolts, which are used to secure loads during lifting or transportation, are often forged to provide the necessary strength and durability. These components must be able to endure significant tension and pressure without compromising their integrity, and forging ensures that they can meet these demands. The use of forged heavy-duty hardware in the tool and hardware industry helps to ensure the safe and efficient movement of materials in demanding environments.
5. Specialized Tools and Custom Forgings
In addition to standard tools and hardware, the forging industry also plays a key role in the production of specialized tools and custom components tailored to specific applications. Many industries require tools that are uniquely designed for their operations, and forging allows manufacturers to create custom solutions that meet the exact specifications of their customers.
For example, mining operations may require specialized tools for breaking rock or drilling deep into the earth, while aerospace companies may need custom fasteners and hardware that can withstand high stress and extreme temperatures. Forging offers the flexibility to produce these specialized components with the necessary strength and performance characteristics. This ability to create customized solutions is particularly valuable in the tool and hardware industry, where precision and reliability are essential.
Companies like Manan Forge, which specialize in producing custom forgings, are well-positioned to serve this need by offering tailored solutions that meet the unique requirements of their clients. By working closely with customers to design and produce forged tools and hardware, these companies can ensure that the final products are optimized for performance, durability, and safety.
6. Environmental and Sustainability Considerations
As industries become more focused on sustainability and reducing their environmental impact, the forging process offers several advantages that align with these goals. Forging is an energy-efficient process that produces minimal waste compared to other manufacturing methods like casting or machining. This is because forging shapes the metal directly, minimizing the need for extensive material removal, which results in less scrap.
In the tool and hardware industry, the durability of forged products also contributes to sustainability by reducing the need for frequent replacements. Tools and hardware made through forging last longer and perform better under harsh conditions, which means less waste and fewer raw materials are required over time. Additionally, many forged components can be made from recyclable materials, further reducing the environmental footprint of the manufacturing process.
As the world continues to shift toward more sustainable practices, the tool and hardware industry is likely to place increasing emphasis on the use of forged products for their environmental benefits. This aligns with the broader trend toward sustainable manufacturing and the growing demand for high-performance, long-lasting tools and hardware that minimize environmental impact.
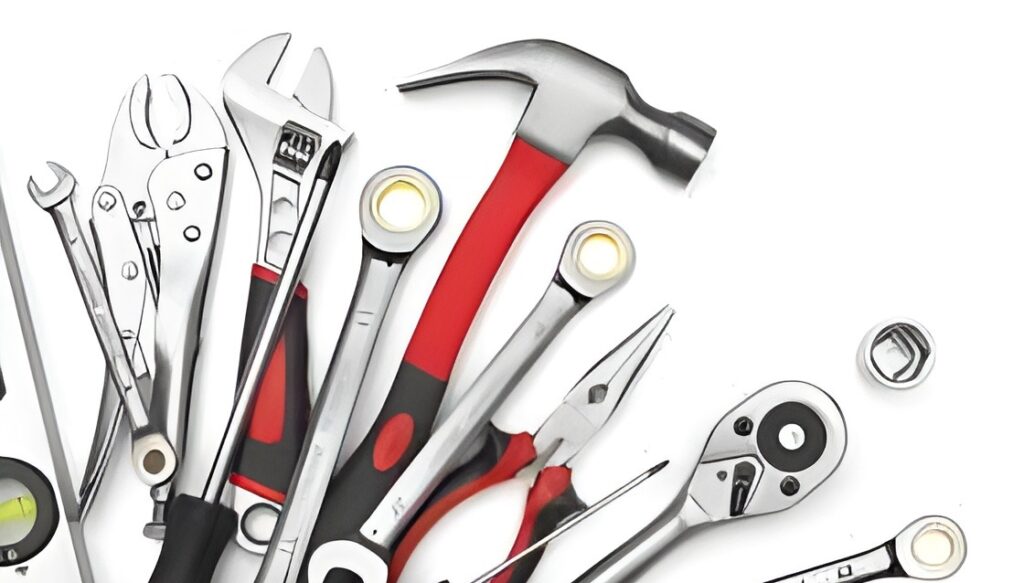
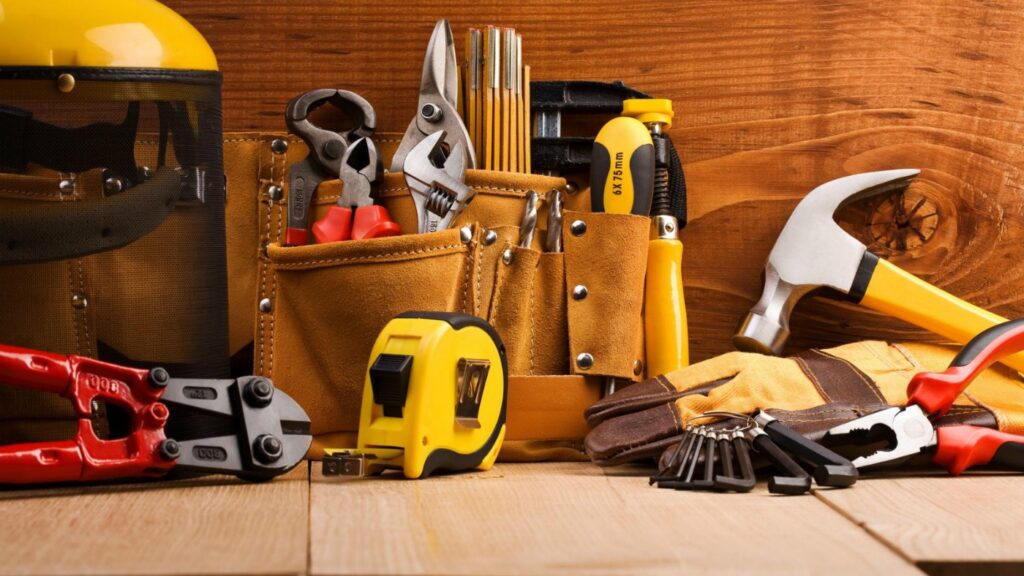
The tool and hardware industry relies heavily on forging for tool and hardware industry components due to their superior strength, durability, and performance across a wide range of applications. From hand tools and fasteners to cutting tools and heavy-duty hardware, forged products are essential for ensuring the reliability and safety of equipment used in construction, manufacturing, automotive repair, and more. The forging process enhances the mechanical properties of these components, making them more resistant to wear, fatigue, and failure, even under extreme conditions. As the industry continues to evolve and the demand for high-performance tools and hardware increases, the role of forging will remain crucial in delivering the quality and reliability that professionals and consumers expect. For companies like Manan Forge, which specialize in producing custom-forged solutions, the tool and hardware industry represents a significant opportunity to provide high-quality products that meet the unique needs of their clients while contributing to the sustainability and efficiency of the sector.