TRANSMISSION INDUSTRY
The transmission industry is a pivotal component of modern machinery and vehicles, facilitating the transfer of power from the engine to the wheels or other machinery elements. This industry spans a wide range of applications, including automotive, aerospace, marine, and industrial systems, where the efficiency and reliability of transmission components are paramount. Within this framework, forging for transmission industry needs plays a crucial role by supplying high-quality forged products that enhance the performance, durability, and overall effectiveness of transmission systems. The forging process, characterized by shaping metal through compressive forces, results in components with superior mechanical properties compared to those produced by other manufacturing methods such as casting or machining. This detailed overview will explore the significant applications of forging for transmission industry requirements, highlighting how forged products contribute to improved efficiency, safety, and sustainability across various transmission systems.
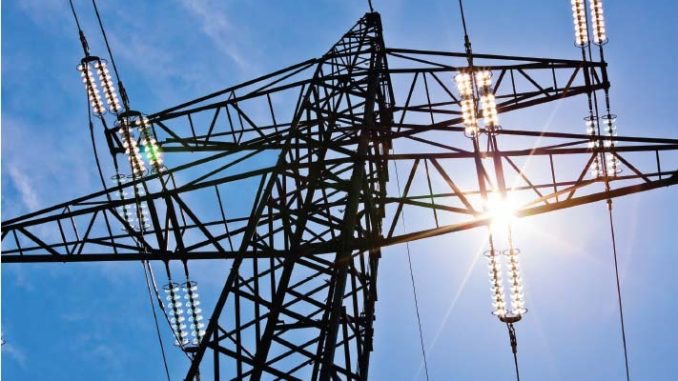
1. Understanding the Forging Process
Forging is a manufacturing process that involves shaping metal through the application of compressive forces, often using hammers or presses. This process can occur at various temperatures—cold, warm, or hot—each offering distinct advantages depending on the desired properties of the final product. The forging process aligns the grain structure of the metal, resulting in components with enhanced strength, toughness, and resistance to fatigue. These attributes are particularly vital in the transmission industry, where components must endure high levels of stress and wear.
The ability to produce forged components with precise dimensions and superior mechanical properties makes forging an ideal choice for critical transmission parts. By leveraging advanced forging techniques, manufacturers can create components that meet the stringent requirements of various applications, ensuring reliability and performance.
2. Forged Components in Automotive Transmissions
In the automotive sector, transmissions play a crucial role in ensuring the efficient transfer of power from the engine to the wheels. Forged components are integral to various transmission systems, including manual, automatic, and continuously variable transmissions (CVTs). Key components such as gears, shafts, and synchronizers are commonly produced through forging, owing to the enhanced strength and durability these processes impart.
Forged gears are particularly important in automotive transmissions, as they must withstand significant forces while maintaining precise engagement with other components. The superior strength and wear resistance of forged gears contribute to the overall efficiency and longevity of the transmission system. Similarly, forged shafts are used to transmit torque between the engine and wheels, ensuring reliable power transfer under varying load conditions. The forging process enhances the fatigue resistance of these shafts, minimizing the risk of failure during operation.
3. Forged Parts in Heavy-Duty Applications
The transmission industry spans beyond automotive applications to include heavy-duty machinery and industrial equipment. Forging for transmission industry needs is essential in these sectors, where transmissions must endure high torque and extreme operating conditions. Examples include construction equipment, agricultural machinery, and marine vessels, where forged gears, shafts, and housings play a crucial role in ensuring reliable performance. In heavy-duty applications, forging for transmission industry requirements provides the strength and durability needed to withstand demanding environments. For instance, in construction equipment, forged gears are designed to handle immense operational forces, ensuring smooth power transmission and minimizing downtime. Additionally, the high strength-to-weight ratio of forged components contributes to improved fuel efficiency, as lighter components reduce machinery weight without compromising performance.
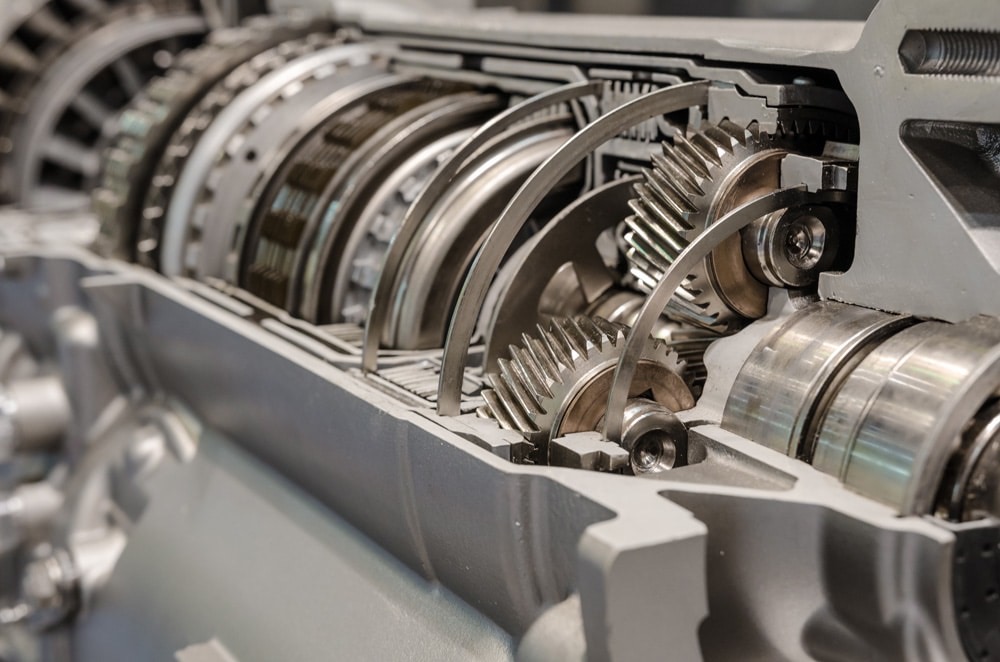
4. Precision and Customisation in Transmission Components
As the transmission industry evolves, there is an increasing demand for precision-engineered components tailored to specific applications. The forging industry is well-equipped to meet these needs, providing custom forged components designed to enhance the performance of transmission systems. By collaborating closely with clients, manufacturers can create components that meet unique specifications and performance requirements.
Custom forging allows for the production of specialized gears, shafts, and housings that are optimized for specific applications, ensuring that transmission systems operate efficiently and effectively. This level of customization enhances the performance of machinery and vehicles, enabling manufacturers to achieve greater operational efficiency and reliability.
5. Durability and Resistance to Wear
In the transmission industry, the durability of components is paramount, as they are subject to continuous wear and tear over time. Forged components exhibit superior resistance to wear and fatigue, making them ideal for use in transmission systems. The forging process produces a fine grain structure that enhances the toughness and strength of the metal, reducing the likelihood of failure during operation.
For instance, forged synchronizers are critical in automotive transmissions, as they facilitate smooth gear changes and prevent grinding during shifts. The durability of these components ensures that transmissions can operate reliably over extended periods, reducing the need for maintenance and repairs. Additionally, the use of forged components minimizes the risk of component failure, which can lead to costly downtime and repairs.
6. Corrosion Resistance in Transmission Applications
Corrosion can pose significant challenges in transmission systems, particularly in environments where exposure to moisture and chemicals is prevalent. Forged components can be produced from corrosion-resistant materials, such as stainless steel or high-strength alloys, ensuring that they remain functional and reliable over time.
The forging process enhances the protective properties of these materials, providing an additional layer of resistance against environmental factors. For example, in marine applications, where transmissions are exposed to saltwater and harsh conditions, forged components offer the durability needed to withstand corrosion and maintain performance. This resistance to environmental degradation is essential for ensuring the longevity and reliability of transmission systems across various industries.
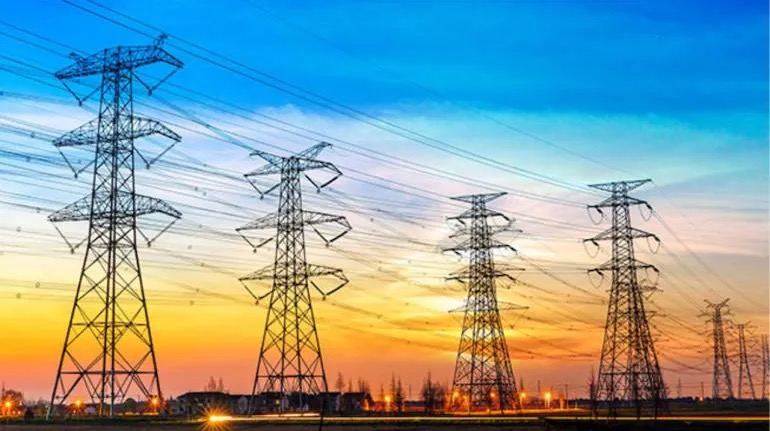
7. Cost Efficiency and Maintenance Considerations
Investing in high-quality forged components can lead to significant cost savings for businesses within the transmission industry. Although the initial investment in forged parts may be higher than alternative manufacturing methods, the long-term benefits often outweigh these costs. The durability and reliability of forged products result in reduced maintenance needs, fewer replacements, and minimized downtime due to equipment failures.
Companies that choose forged components can benefit from extended service life and improved operational efficiency. This longevity ensures that transmission systems remain in service longer, leading to greater productivity and profitability for businesses. Additionally, the reduced frequency of repairs and replacements translates to lower overall maintenance costs, further enhancing the cost-effectiveness of forged products.
8. Innovation in Forging Technology
The forging industry is continually evolving, with advancements in technology driving improvements in efficiency, quality, and performance. Modern forging processes utilize computer numerical control (CNC) machines and automated systems to increase precision and reduce production times. This technological advancement enables manufacturers to produce high-quality forged components more efficiently while minimizing waste.
Innovations in material science also play a crucial role in the forging industry, leading to the development of new alloys and composites that enhance the performance of transmission components. By leveraging these advancements, manufacturers can create forged products that are lighter, stronger, and more resistant to wear and corrosion, further expanding the applications for forged components in the transmission industry.
9. Quality Assurance in Forged Transmission Components
Ensuring the quality and reliability of forged components is paramount in the transmission industry, where failures can lead to safety risks and significant financial losses. Forging manufacturers adhere to stringent quality control measures and industry standards to ensure that their products meet the necessary performance and safety requirements.
Quality assurance processes often involve rigorous testing protocols, including tensile testing, hardness testing, and dimensional inspections. By implementing these measures, manufacturers can guarantee the reliability of their forged components, instilling confidence in customers that they are investing in products that will perform effectively under demanding conditions.
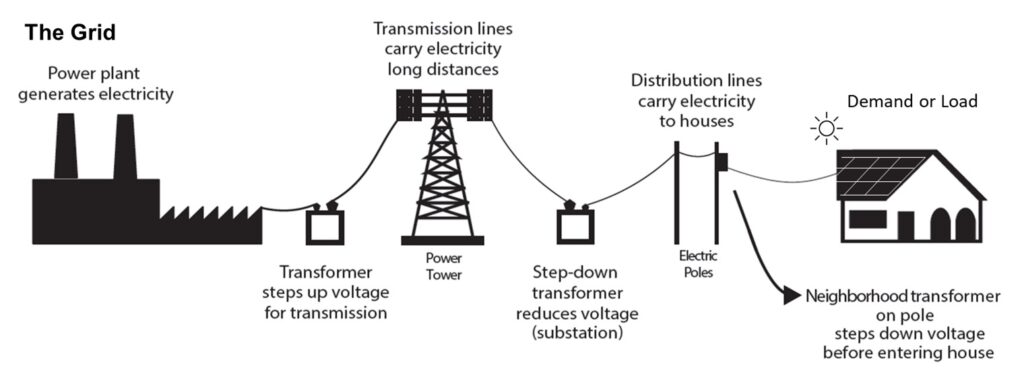
7. Cost Efficiency and Maintenance Considerations
As industries increasingly focus on sustainability, the forging industry is also adapting to meet these challenges. Forging processes are generally more environmentally friendly than other manufacturing methods, producing less waste and requiring less energy. Additionally, many forging companies are exploring ways to utilize recycled materials in the production of forged components, contributing to a more sustainable manufacturing process.
By choosing forged components, businesses in the transmission industry can benefit from the durability and longevity of these products, leading to fewer replacements and reduced material waste. This aligns with the growing emphasis on sustainable practices in manufacturing and helps companies achieve their environmental goals.
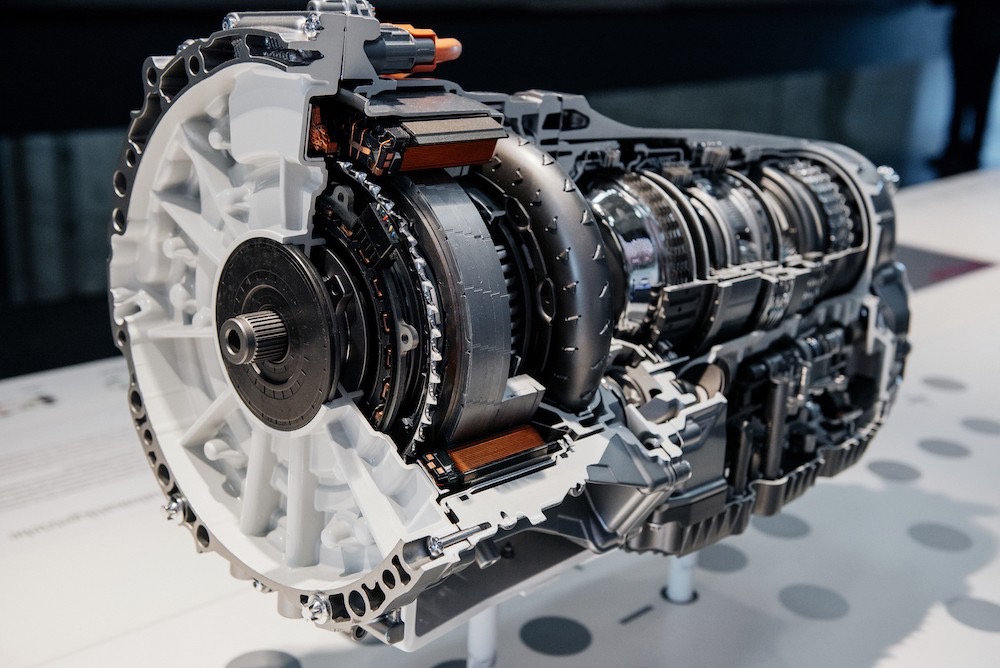
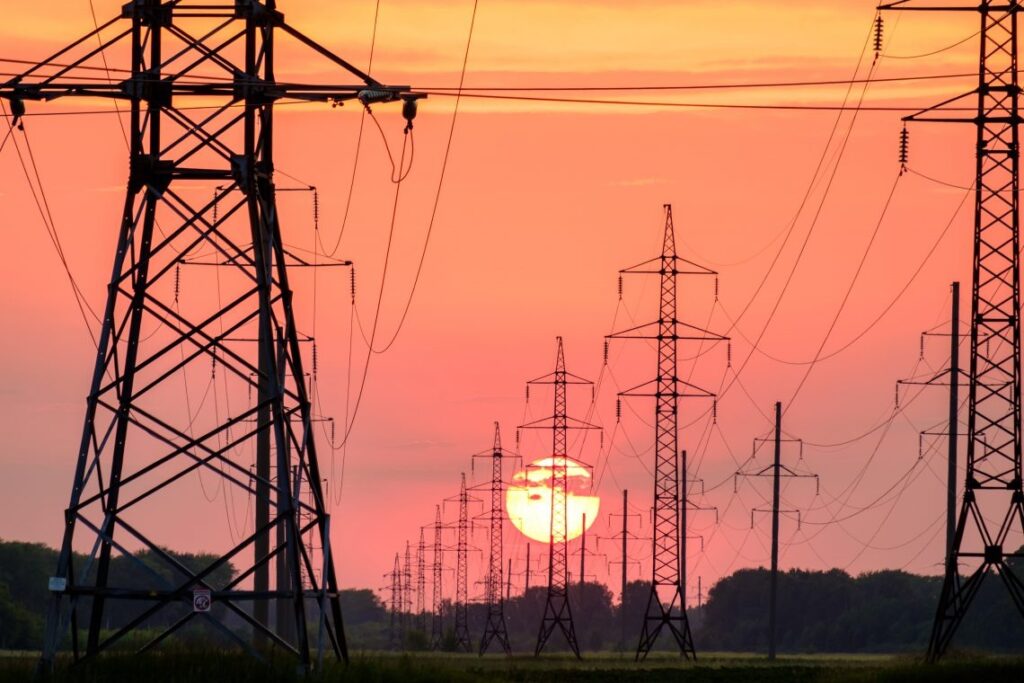
So, The forging industry plays a critical role in supporting the transmission sector by providing high-quality components that enhance the performance, reliability, and efficiency of transmission systems. Forged products, including gears, shafts, synchronizers, and housings, are essential for meeting the demands of modern automotive and industrial applications. As the transmission industry continues to evolve, the importance of forged components will only increase.
By choosing forged products, businesses can benefit from improved durability, reduced maintenance costs, and enhanced productivity. The flexibility of the forging process allows for custom solutions tailored to specific transmission needs, ensuring that equipment operates at optimal levels. As innovations in forging technology continue to advance, the industry will remain a vital partner in the transmission sector, driving growth, sustainability, and efficiency in power transfer applications. For companies like Manan Forge, which specialize in producing forged solutions for the transmission industry, the opportunities to contribute to the sector’s success are significant and promising.