AEROSPACE INDUSTRY
The Role of Forging in the Aerospace Industry
Forging has been a fundamental process in manufacturing for centuries, and in modern times, its importance has grown even more, especially within highly demanding sectors such as aerospace. The aerospace industry, which is synonymous with precision, reliability, and safety, relies heavily on forging for aerospace industry applications to produce critical components. These parts must meet stringent standards for performance, strength, and durability, all while maintaining lightness to support fuel efficiency and overall flight performance. The forging for aerospace industry meets these needs by producing high-quality, high-strength components essential to aircraft safety, engine performance, and the structural integrity of space exploration equipment.
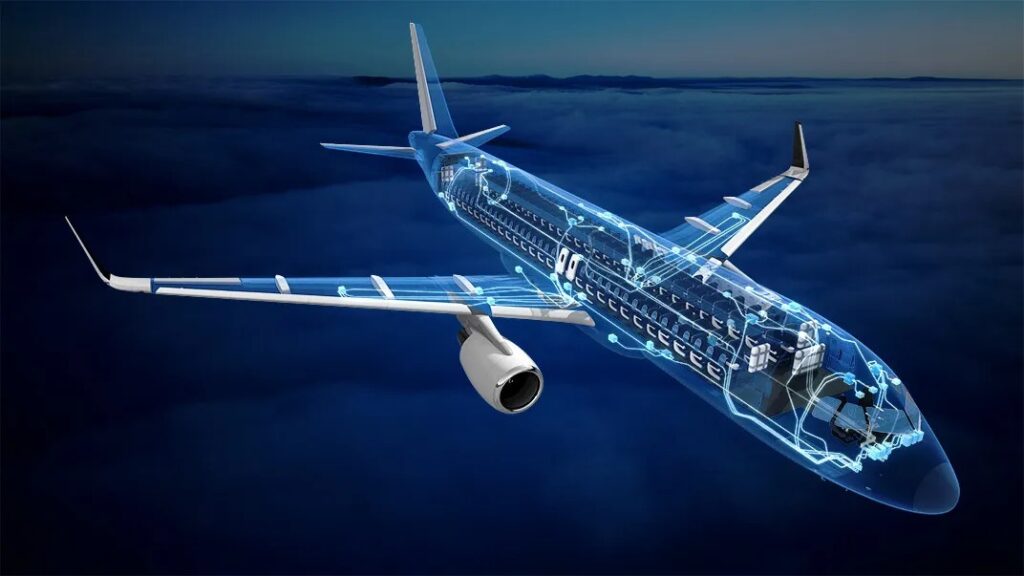
Why Forging?
Forging for aerospace industry applications involves shaping metal under high pressure to create parts with significantly greater strength than those produced through other methods, like casting or machining. The mechanical properties achieved through forging for aerospace industry parts—such as strength, ductility, toughness, and fatigue resistance—are essential for applications where materials face high stresses and extreme conditions. Unlike casting, where material flows into a mold, forging for aerospace industry components compacts the metal, aligning its grain structure to boost strength, fatigue resistance, and wear resistance, making it ideal for demanding aerospace uses.
In aerospace, forged parts are typically manufactured using high-performance metals and alloys, such as titanium, aluminum, steel, and superalloys, which offer the necessary strength-to-weight ratio and durability. These materials are chosen not only for their mechanical properties but also for their ability to withstand extreme temperatures, as many aerospace components operate in high-heat environments, such as jet engines.
Applications of Forged Products in Aerospace
Aerospace components are incredibly diverse, ranging from small fasteners to massive structural elements. Forged parts are used extensively in both aircraft and spacecraft, covering a wide range of applications:
1.Aircraft Engines
One of the most critical applications of forging in aerospace is in the manufacture of aircraft engines. Components such as turbine blades, compressor disks, and shafts are all forged due to the extreme mechanical stresses they must endure. These parts operate at high speeds and temperatures, requiring materials that not only withstand the rigors of flight but also maintain structural integrity over time. Forged turbine blades, for example, can endure the immense centrifugal forces of spinning at thousands of revolutions per minute, as well as the high temperatures generated during combustion.
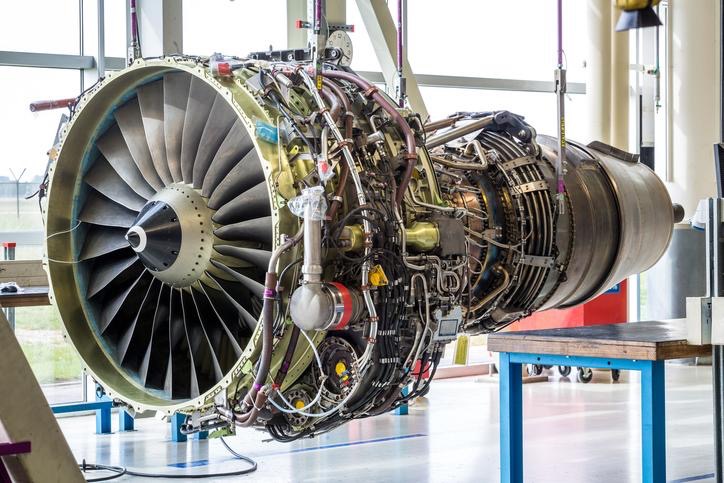
2.Landing Gear
The landing gear system of an aircraft is another area where forging is indispensable. The landing gear is subjected to enormous stress, especially during takeoff and landing. Forged components ensure that these parts have the necessary strength to withstand these forces without failure. Parts like axles, struts, and joints are forged to provide the optimal balance of strength and weight, ensuring the safety and performance of the landing system. Given the safety-critical nature of landing gear, forged components are rigorously tested to meet industry regulations and standards.
3.Structural Components
Forging is also used in the production of key structural components, such as wing spars, fuselage frames, and bulkheads. These parts are essential to the integrity and stability of the aircraft. Forged parts in this application offer better fatigue resistance and strength compared to other manufacturing methods, ensuring that the aircraft can withstand the aerodynamic forces it experiences during flight. Furthermore, the use of lightweight alloys in forgings helps reduce the overall weight of the aircraft, improving fuel efficiency and performance.
4.Fasteners and Connectors
Aerospace applications also rely on forged fasteners and connectors, which must meet exacting standards for strength, weight, and corrosion resistance. Fasteners made from high-performance alloys are used throughout the aircraft, from the engine to the airframe, and they are designed to resist loosening or failure under the severe vibrations and temperature fluctuations experienced during flight.
5.Spacecraft Components
Beyond aircraft, the forging industry plays a key role in space exploration as well. Spacecraft require components that are lightweight yet incredibly strong, as they must endure the extreme conditions of space travel. Forged parts, such as rocket engine components, structural support elements, and fasteners, are critical to the success of space missions. The extreme environments of space—vacuum, radiation, and extreme temperatures-demand the use of advanced materials and manufacturing processes, and forging is able to meet these challenges head-on.
Advantages of Forged Products in Aerospace
The aerospace industry has a unique set of requirements, and forged products offer several advantages that make them ideally suited for these applications:
1. Superior Strength and Durability
Forged components are inherently stronger than cast or machined parts because the forging process compresses the metal, creating a dense grain structure. This results in improved strength, fatigue resistance, and toughness, which are crucial in aerospace applications where materials are subjected to extreme forces and high-stress environments.
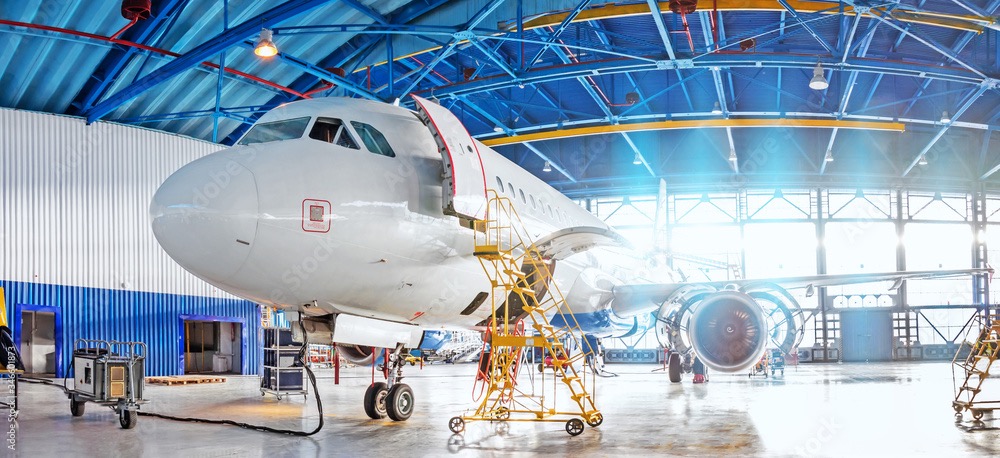
2. Lightweight Components
One of the critical goals in aerospace design is to reduce the weight of aircraft and spacecraft, as lighter vehicles are more fuel-efficient and cost-effective to operate. Forging allows for the use of high-strength materials like titanium and aluminum, which offer excellent strength-to-weight ratios. These materials are capable of providing the necessary performance while minimizing the overall weight of the aircraft or spacecraft.
3. Enhanced Fatigue Resistance
Aerospace components are often subjected to cyclical loading, meaning they experience repeated stress over the course of their use. Forged parts have superior fatigue resistance due to their refined grain structure, which minimizes the risk of failure over time. This is especially important for parts like landing gear or engine components that experience significant stresses during every flight cycle.
4. Precision and Customisation
The aerospace industry demands precision in every aspect of its manufacturing process. Forging can achieve high levels of accuracy and repeatability, ensuring that parts meet exact design specifications. In addition, forging can be used to create custom parts that meet specific aerospace requirements, including complex geometries and unique material properties. This flexibility is essential for producing components that can withstand the unique challenges of aerospace environments.
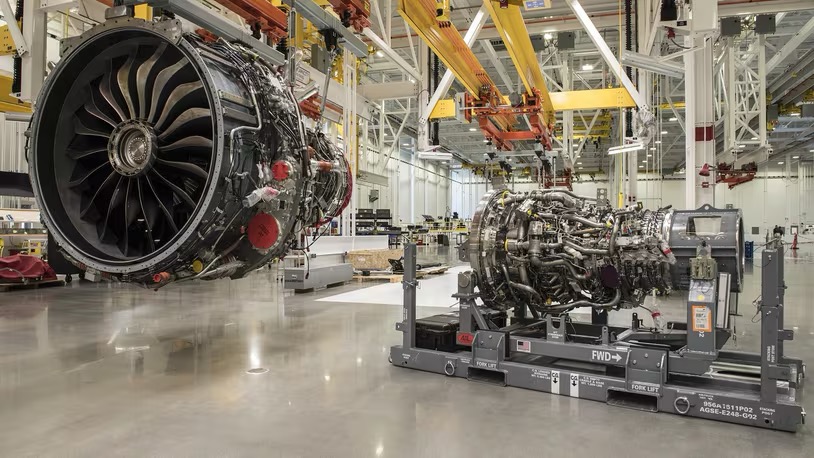
5. Cost-Effective Manufacturing
While forging is often seen as a premium manufacturing process, its durability and strength can actually make it a more cost-effective solution over the long term. Forged parts typically have longer lifespans and require less maintenance than components made through other methods. This reduces downtime and operational costs for aerospace companies, contributing to overall efficiency and cost savings.
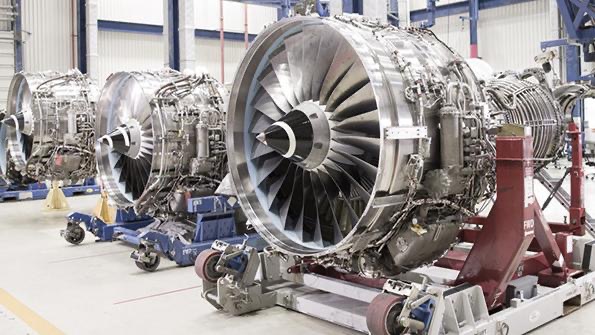
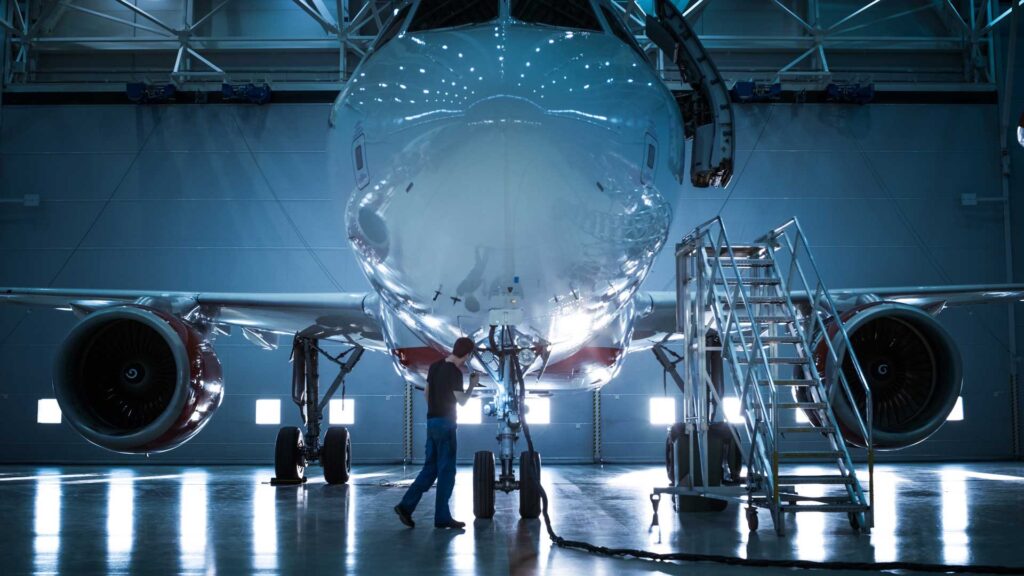
As a company like Manan Forge continues to expand its capabilities, the demand for customized forgings in aerospace has grown significantly. Aerospace manufacturers often require specialized parts that meet highly specific performance criteria, and custom forging solutions allow for the production of components tailored to these exact needs. From material selection to the design and forging process, Manan Forge can provide the flexibility and expertise needed to meet the precise demands of aerospace clients.
By leveraging advanced forging techniques, Manan Forge can contribute to innovations in the aerospace industry, providing components that enhance aircraft performance, reduce fuel consumption, and improve overall safety. These components are not only critical to current aerospace operations but also to the future of the industry as it moves toward new advancements, such as more fuel-efficient engines, electric aircraft, and deep space exploration.